Simulator features
The simulator allows you to complete the following training programs without the need to send trainees to existing platforms:
Platform equipment
Study the composition and layout of offshore platform equipment
Navigation bridge
Study the composition and purpose of control posts of the navigation bridge of offshore platform
Maneuvering
Acquire skills in maneuvering the offshore platform taking into account changing sailing conditions
Ballast operations
Study the theory and train ballasting/deballasting operations of offshore platform to ensure the required stability
Anchor winches
Learn to control platform anchor winches in order to set up a given point, hold and remove it from a given point without the help of support vessels
Supply vessels
Practice interaction with supply vessels
Delivery
The simulator is supplied under a license agreement in the form of electronically transmitted software with a perpetual, non-exclusive license. The simulator software includes:
- Displays of control stations of the offshore platform navigation bridge as described below
- Mathematical model of hydrostatics and hydrodynamics of offshore platform with taking into account various possible sailing conditions
- 3D visualization of the sailing area for various weather conditions and time of day
- Functions for managing the learning process – start/stop/pause the simulator; select / load / exercise modification; recording of an exercise and subsequent viewing of completed records exercises for the purpose of their analysis and discussion (debriefing)
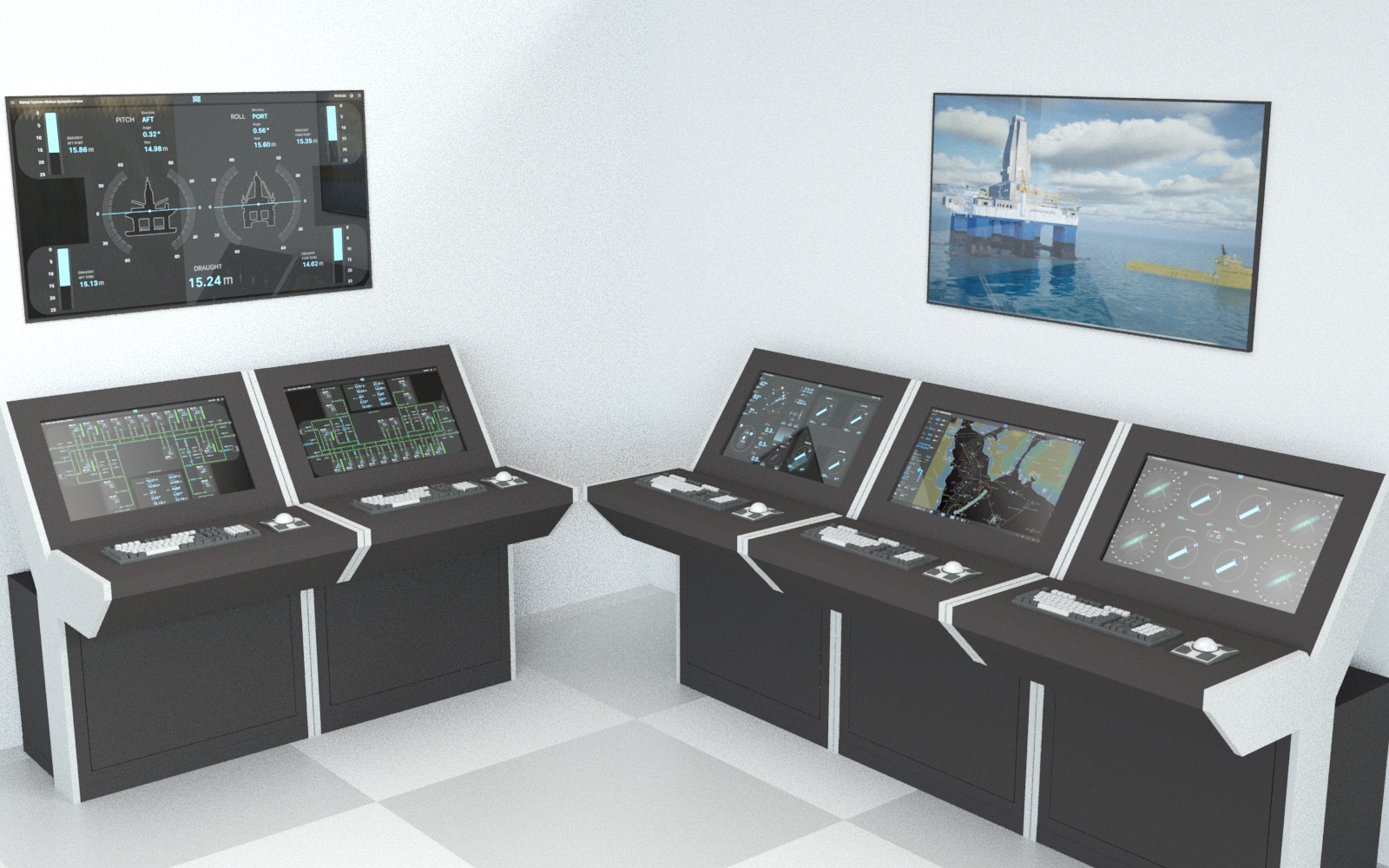
Simulator configuration
Delivery package
The minimum delivery package includes the following workstations:
- Visualization system PC with a monitor of at least 32” (min. 1)
- PC with two monitors for coning panel and maneuvering panel
- PC with monitor for electronic navigational chart
- PC with monitor for controlling anchor winches
- PC with two monitors for monitoring ballast tanks and controlling ballast pumps and valves
The simulator documentation includes a detailed description of the set of exercises for practicing the above skills.